Q&A: Kai Berszuck provides insights into the production department
Welcome to our employee interview series – with Kai Berszuck
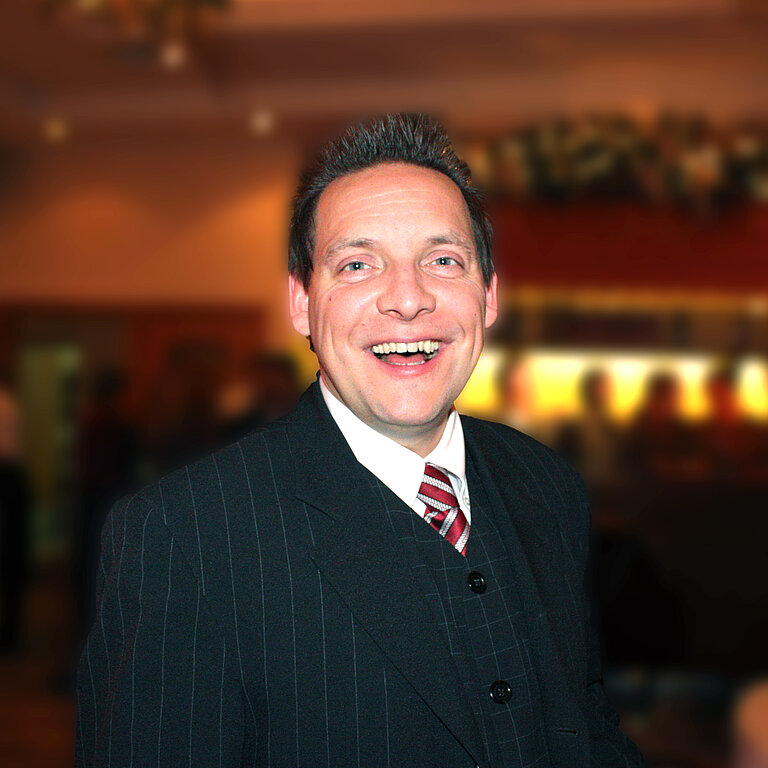
Plasmatreat is more than just a workplace for me. It's a place where I've been able to grow, create new things, and shape the future together with great colleagues.

What were your first impressions when you joined the company?
It happened really quickly back then – I had barely introduced myself when I was already employed. That was in 1998, so it was quite a while ago. We were just eight or nine people at the Bisamweg site back then – so it was really small. I jumped straight in, was immediately part of the service team and went straight out to visit customers. My colleague Markus Thiel took me by the hand and showed me everything. I quickly learned what was important - and was soon able to drive to service jobs on my own.
How do you think the company has changed over the last 30 years?
Rapidly! The development is really impressive. When I think that we started with eight people and now have 300 employees worldwide with 25 locations, that's incredible.
What was the most challenging project you worked on and what did you learn from it?
In 2010, when we took over a company in the USA and integrated it into our own subsidiary there. I was in San Francisco for nine months at the time. The systems there were originally only intended for the US market and did not meet international standards. Together with the team led by Markus Thiel and Guido Marks from the design department, we revised the technology so that we could sell it worldwide.
What successes or achievements make you particularly proud?
Firstly, of course, the project in the USA - something small and immature for local conditions was turned into a system that meets international standards for worldwide sales. But also the many situations in customer service where I was able to help directly - these were often challenging moments. Having mastered these challenges makes me proud.
How would you describe the corporate culture?
Familiar - as much as possible. Of course, this changes with size, but the management makes every effort to maintain this culture. What I particularly appreciate: People discuss things openly, even if they have different opinions - and then move forward into the future together. And in my group in particular, in electrical production, the team spirit is enormous. Especially when things get tight, you stand up for each other.
Were there any mentors or role models in the company who inspired you?
Yes, definitely. Christian Buske with his visions – we've known each other for over 37 years, we were already pulling cables together back then. And Holger Timpe - as a master craftsman, he was always at the forefront. I learned a lot from him.
How have your tasks and responsibilities changed over the years?
I started in service and was on the road a lot. Later, I withdrew from this somewhat and was only involved in special cases - such as PlasmaPlus® – during service calls. Today I'm in a kind of special department where everything that is “special” ends up. I still really enjoy it and I don't want to do anything else.
I also help out in research from time to time when I'm needed, e.g. supporting test systems. And: I co-founded the works council about 20 years ago - that was also an important step for me and the company.
What do you wish for the future of the company?
I would like to retire here – so I hope that I can also celebrate my 35th anniversary. But I am confident: we are broadly and innovatively positioned.
What advice would you give new employees?
Be open! If there are challenges – ask colleagues who have been with us for a long time. They know how things work. And: take advantage of the management's openness - it's there and should be used. Loyalty, honesty and openness – that really gets you far here.
What else would you like to learn?
There's always room for improvement in technical terms – for example in the area of design. And I see myself as a point of contact for my colleagues across departments. I've been here for so long – I definitely want to pass on and share my knowledge.